現場主義を徹底した設計・生産体制
- HOME
- 現場主義を徹底した設計・生産体制
当社はトヨタ関連企業様への生産設備の納入実績が豊富であり、その経験を通じて高い技術力を蓄積してきました。お客様のニーズを的確に捉え、最適なソリューションを提供することで、信頼と成果を築いています。
ケーエスジーの考える「現場主義」
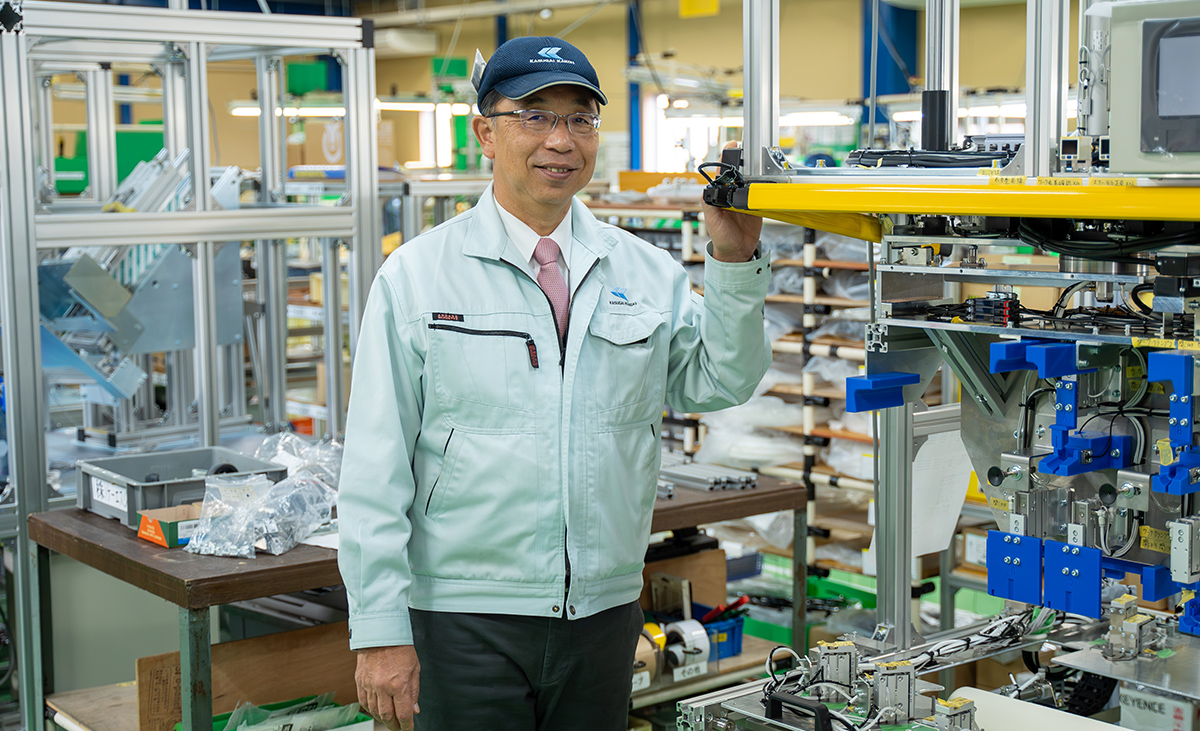
ケーエスジーは、トヨタ関連企業への装置や部品の納入実績を通じて蓄積された経験と技術力を基盤に、現場主義を徹底しています。
当社では、現場の声を最優先に捉え、実際の生産プロセスで発生する課題に即応できる柔軟な対応力を持っています。この「現場第一主義」は、単に現場に目を向けるだけでなく、現場で働く人々の視点に立った課題解決を追求する姿勢を指します。
生産ライン全体、各工程の要素を見据えた装置を設計することで、追加工や納入後の改造が不要な装置を提案を意識しています。
現場主義の中核をなすのが「トヨタ生産方式(TPS)」に基づく考え方です。
この考え方により、ムダの排除や生産性向上を可能にし、持続可能な成長とお客様の競争力強化に寄与しています。
現場主義のベースにあるTPS(トヨタ生産方式)とは?
トヨタ生産方式(TPS)は、トヨタ自動車が開発した世界的に評価の高い生産方式であり、ケーエスジーの生産体制の基盤にもなっています。
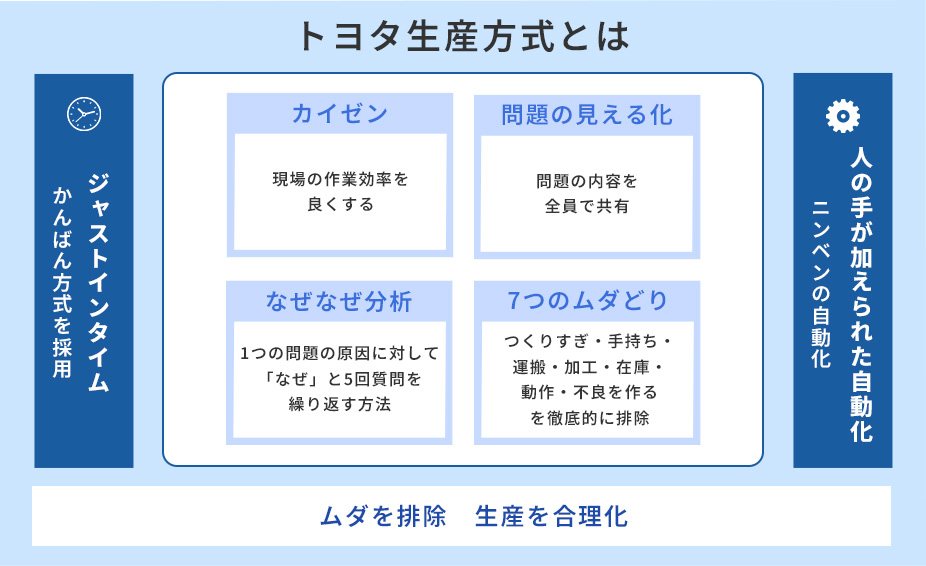
-
ジャストインタイム
必要なものを、必要なときに、必要な量だけ生産する仕組みです。これにより、在庫を最小化しながら効率的な生産を実現しています。ケーエスジーでは、この原則をもとに、納期遵守や生産リードタイム短縮に取り組んでおり、お客様の期待に応えるための柔軟な供給体制を構築しています。
-
自働化
機械が故障や異常を自動的に検知し、必要に応じて人が介入する仕組みです。この原則により、不良品の発生を抑え、生産ラインの安定化が図られます。ケーエスジーでは、設備の選定や運用においてこの自働化の考えを徹底し、最適な設備提案を行うことで、お客様の生産効率向上に貢献しています。
TPSは、「カイゼン」や「ムダの排除」を基本理念としており、当社はこれらの理念を実際の業務プロセスに適用することで、効率的で高品質な製品を提供しています。
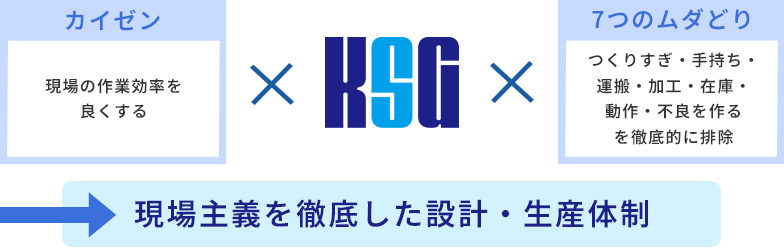
ケーエスジーの徹底Point
徹底Point❶ 風通しのよさを活かしたカイゼン
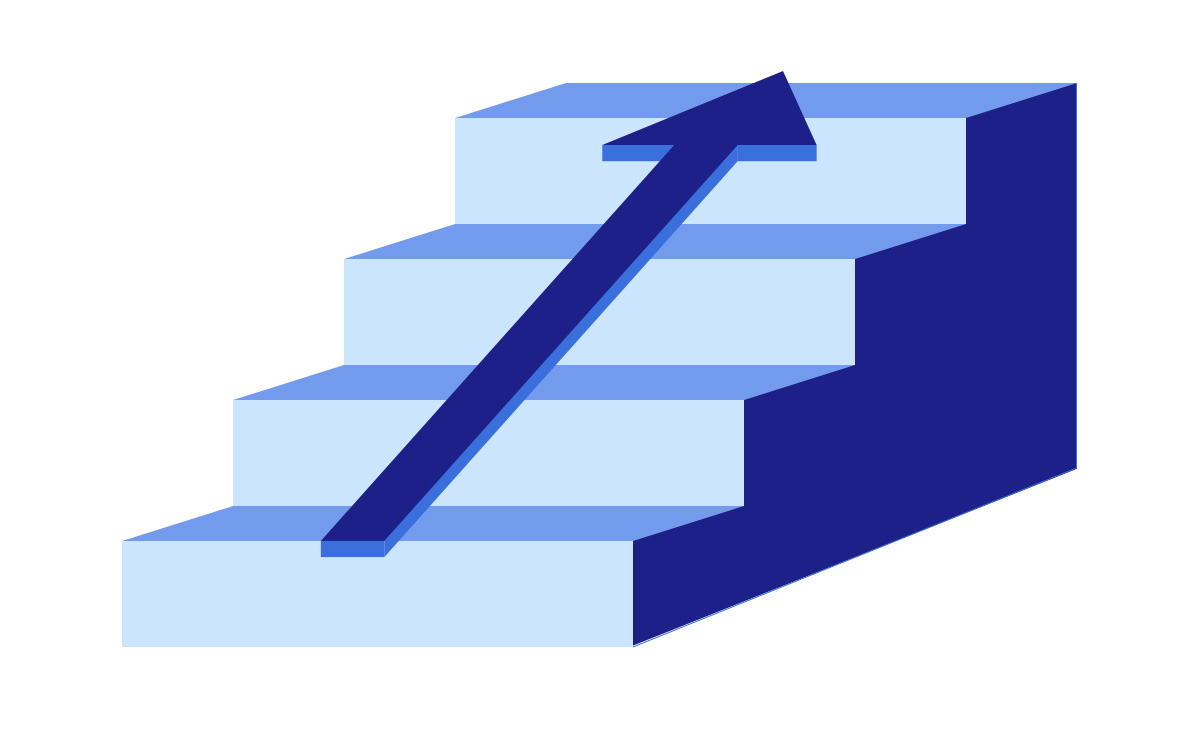
ケーエスジーは、カイゼン活動を通じて、製造現場における継続的な改善を進めています。生産プロセスの中で見つかった課題を即座に設計や社内全体で共有し、全員参加型の改善活動を実施しています。このようなカイゼンの取り組みにより、ムダを徹底的に排除し、効率を最大化するだけでなく、作業環境の安全性や従業員の働きやすさも向上させています。
徹底Point❷ 3Sによるムダの発見
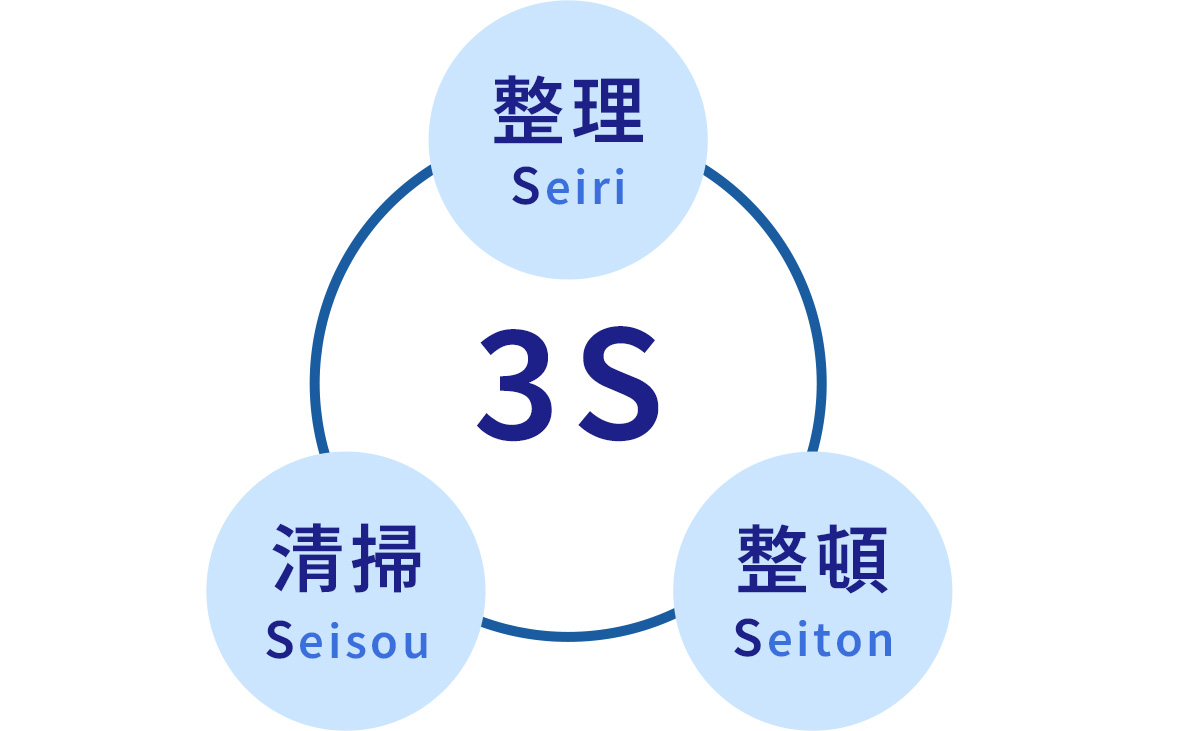
ケーエスジーでは、3S(整理・整頓・清掃)を徹底することでムダを特定し、それを取り除くための具体的なアプローチを実施しています。これには、作業手順の見直しや設備の最適化が含まれます。また、グループ会社との連携により、ムダの発生を未然に防ぐ仕組みを構築し、持続可能な生産体制を実現しています。
徹底Point❸ 社内プロセスの標準化
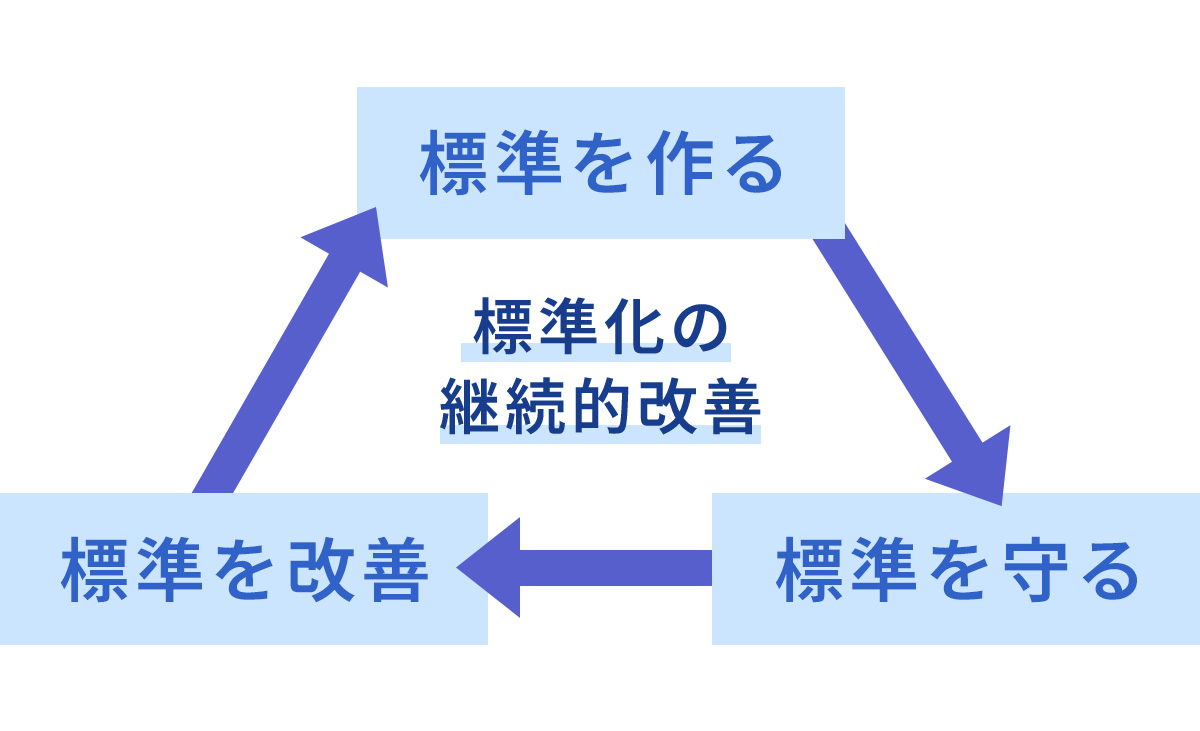
カイゼンとムダを徹底することで、設計・製造プロセスの最適化を行うことが可能です。
この最適なプロセスをしっかりと標準化することで、一過性の取り組みではなく、会社の資産・ノウハウとして蓄積しています。
安定した品質の設備を、お客様納品する設計・生産体制には社内プロセスの標準化が重要です。
また、標準化することで、カイゼン・ムダに関する取り組みも加速させることが可能です。
設計・製造提案事例
-
-
課題表皮巻き工程終了後、設備前面からワークを取り出し、後工程へ手動で搬送していたため、作業者の工数と移動負担が大きかった。
-
カイゼン表皮巻き機の側面壁を撤去し、ワークがそのまま後工程にスムーズに渡せる導線設計に変更。
前後工程を考慮したレイアウトの見直しを実施。 -
ムダ・ワーク取出し時の移動時間
・設備前面と側面を行き来する手間
・作業範囲が広くなることでの負担増
これまで表皮巻きが完了したワークは、設備の正面から手作業で取り出し、後工程へ運んでいました。
しかしこの工程では、作業者が都度移動する必要があり、時間的ロスと身体的負担が大きい状態でした。
今回、設備の側面を開放し、後工程との接続を可能にしたことで、ワークの取り出しから次工程への受け渡しまでがスムーズになり、作業導線が大幅に短縮されました。≪ 改善ポイント ≫
・側面開放によるワーク搬送導線の最適化
・工程間のスムーズな連携により作業時間を短縮
・作業者の移動距離と負担の軽減
・工程間の属人性を排除し、自動化への対応も視野に -
-
-
課題車載用カップホルダーの表皮巻き工程を手作業で対応していたため、作業者に大きな負担がかかっていた。
-
カイゼン表皮巻き機の導入により、手作業を自動化。安定した品質と生産性を両立し、作業負荷を軽減。
-
ムダ・付加価値の低い単純作業を人手で対応
・作業者の疲労による品質のばらつき
・工程ごとの属人性による生産効率の低下
カップホルダーの表皮巻き工程では、従来、熟練作業者が一つひとつ手作業で対応しており、時間と労力を要していました。
作業内容は単純ながらも繰り返しが多く、長時間の作業による疲労が蓄積しやすい工程でもありました。
そこで当社では、表皮巻き専用の自動機を導入・提案し、作業の大幅な効率化を実現。品質のばらつきを抑え、誰でも安定した作業ができる体制を構築しました。
≪ 改善ポイント ≫
・自動機による作業負担の軽減
・作業者の疲労リスクと属人性の排除
・生産性・品質の安定向上
・手作業からの脱却による付加価値向上とリソース最適化 -
-
-
課題バッテリーホースの製造において、3つの単純作業工程を個別に手作業で行っていたため、多くの作業者が必要となり、作業効率も悪く、工程ごとにスペースと中間材料を多く消費していた。
-
カイゼン各作業の詳細分析を行い、それらを一括で処理できる一気通貫の自動化設備を開発。省人化と省スペース化を同時に実現。
-
ムダ・単純作業に人員を多く割く非効率
・工程間ごとの搬送・待機に伴うスペースの無駄
・中間在庫の過剰保有による管理負荷
バッテリーホースの加工では、3つの単純工程をそれぞれ手作業で実施しており、1日あたり平均2.6名の作業者が必要でした。
また工程ごとの作業スペースや中間材料の仮置き場所も多く必要で、生産効率が課題となっていました。
そこで、各工程を詳細に分析したうえで、それらを一台の装置に集約し、連続処理できる一気通貫型の自動化設備を導入。
結果として、必要人員を2.6名/日 → 1名/日へ削減し、作業スペースも大幅に縮小。現場のムダを徹底的に排除しました。
≪ 改善ポイント ≫
・工程全体を一台で処理する自動化構想
・工数削減と作業負担の大幅軽減
・中間材料とスペースの最適化
・省人化と生産性向上を両立するレイアウト設計 -